What is Porosity in Welding: Vital Tips for Achieving Flawless Welds
What is Porosity in Welding: Vital Tips for Achieving Flawless Welds
Blog Article
Porosity in Welding: Identifying Common Issues and Implementing Best Practices for Prevention
Porosity in welding is a prevalent problem that frequently goes unnoticed till it triggers considerable issues with the honesty of welds. In this discussion, we will discover the crucial elements contributing to porosity development, examine its destructive impacts on weld performance, and review the finest practices that can be taken on to reduce porosity occurrence in welding procedures.
Common Reasons For Porosity
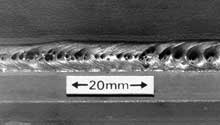
Using unclean or wet filler materials can present contaminations into the weld, adding to porosity problems. To minimize these usual causes of porosity, comprehensive cleaning of base metals, appropriate securing gas option, and adherence to optimum welding criteria are important methods in attaining premium, porosity-free welds.
Effect of Porosity on Weld Top Quality

The existence of porosity in welding can considerably compromise the architectural honesty and mechanical residential properties of welded joints. Porosity creates spaces within the weld metal, compromising its overall strength and load-bearing capacity.
Welds with high porosity levels have a tendency to show reduced effect strength and lowered capability to flaw plastically before fracturing. Porosity can restrain the weld's capability to effectively transfer pressures, leading to early weld failing and possible safety hazards in vital structures.
Finest Practices for Porosity Prevention
To enhance the structural integrity and top quality of bonded joints, what click here for more info certain steps can be executed to reduce the occurrence of porosity throughout the welding procedure? Utilizing the appropriate welding technique for the details product being welded, such as adjusting the welding angle and weapon placement, can additionally avoid porosity. Regular click for source examination of welds and prompt remediation of any concerns determined during the welding procedure are necessary methods to prevent porosity and generate top notch welds.
Significance of Proper Welding Strategies
Carrying out proper welding techniques is vital in ensuring the structural stability and top quality of welded joints, developing upon the structure of reliable porosity prevention steps. Extreme warmth can lead to increased porosity due to the entrapment of gases in the weld pool. Furthermore, making use of the suitable welding criteria, such as voltage, existing, our website and travel speed, is important for attaining audio welds with marginal porosity.
Furthermore, the option of welding process, whether it be MIG, TIG, or stick welding, must straighten with the details requirements of the project to guarantee ideal outcomes. Appropriate cleansing and prep work of the base steel, along with picking the appropriate filler product, are also important components of skilled welding methods. By adhering to these finest methods, welders can lessen the danger of porosity formation and create premium, structurally audio welds.
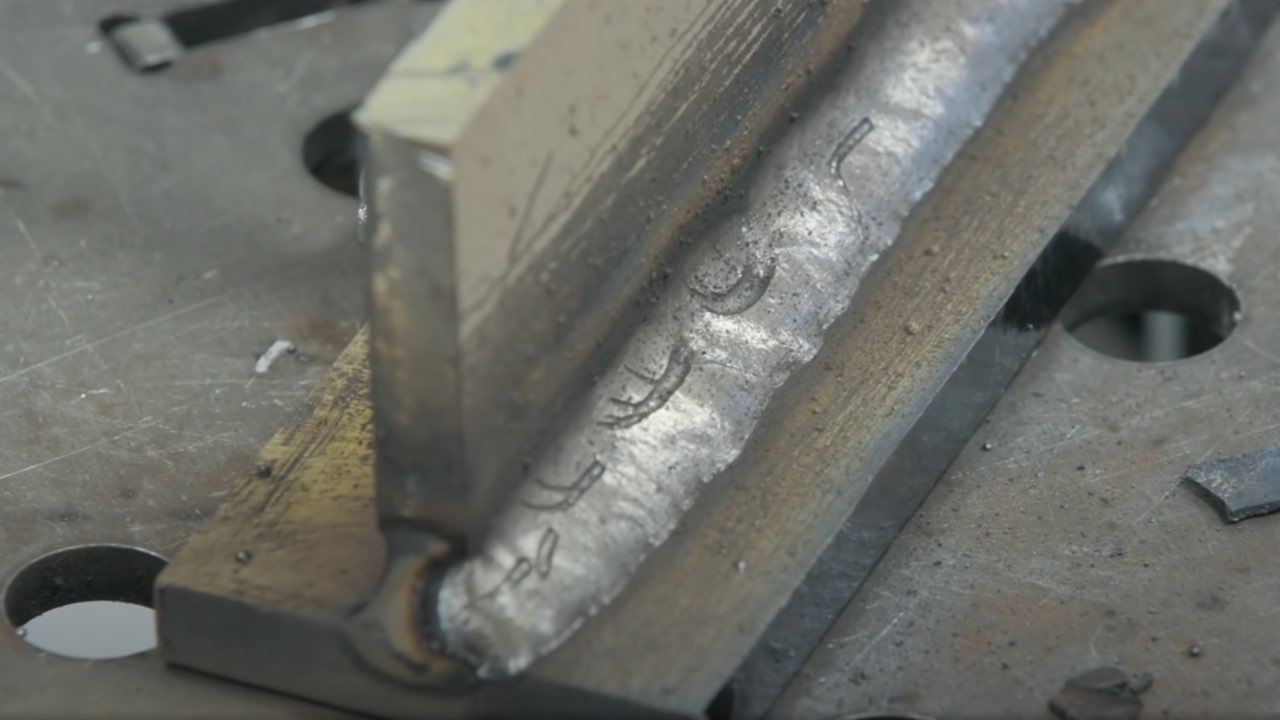
Evaluating and High Quality Control Procedures
Evaluating procedures are important to spot and prevent porosity in welding, ensuring the toughness and longevity of the last item. Non-destructive testing techniques such as ultrasonic screening, radiographic testing, and visual inspection are frequently utilized to determine potential issues like porosity.
Post-weld assessments, on the other hand, evaluate the last weld for any type of flaws, consisting of porosity, and confirm that it satisfies defined criteria. Executing an extensive high quality control strategy that includes extensive screening treatments and inspections is vital to lowering porosity problems and making sure the total top quality of bonded joints.
Conclusion
Finally, porosity in welding can be a common problem that affects the high quality of welds. By determining the typical sources of porosity and applying ideal practices for avoidance, such as correct welding techniques and testing steps, welders can make sure high top quality and trusted welds. It is vital to prioritize prevention methods to minimize the occurrence of porosity and maintain the integrity of welded structures.
Report this page